Introduction
A material takeoff, or quantity takeoff, is a crucial document in the construction industry. It provides a detailed list of all materials required for a project, from the largest structural components to the smallest fasteners. An accurate takeoff ensures that the project stays on budget and schedule. In this blog post, we’ll delve into the key elements of a comprehensive material takeoff.
Understanding the Importance of a Material Takeoff
Before we dive into the specifics, let’s understand why a material takeoff is so critical:
- Accurate Cost Estimation: A detailed takeoff helps in precise cost estimation for the project.
- Efficient Procurement: By identifying material requirements upfront, procurement can be planned efficiently.
- Reduced Waste: A well-prepared takeoff minimizes material wastage.
- Smooth Project Execution: A comprehensive takeoff ensures that all necessary materials are available when needed.
Essential Components of a Material Takeoff:
Here’s a breakdown of what goes into a cost estimate:
Project Details:
- Project name
- Location
- Date of takeoff
- Prepared by
Drawing and Specification References:
- List of all drawings and specifications used for the takeoff.
Material Categories:
- Organize materials into clear categories like concrete, steel, wood, electrical, plumbing, etc.
Detailed Quantity Calculations:
- Accurately calculate quantities for each material item, including dimensions, units, and total quantities.
Material Descriptions:
- Provide clear and specific descriptions of materials, including grades, sizes, and specifications.
Unit Prices:
- Include unit prices for each material item, if available.
Total Material Costs:
- Calculate the total cost of materials based on quantities and unit prices.
Labor Estimates:
- While not strictly a material takeoff component, labor estimates can be included for overall project planning.
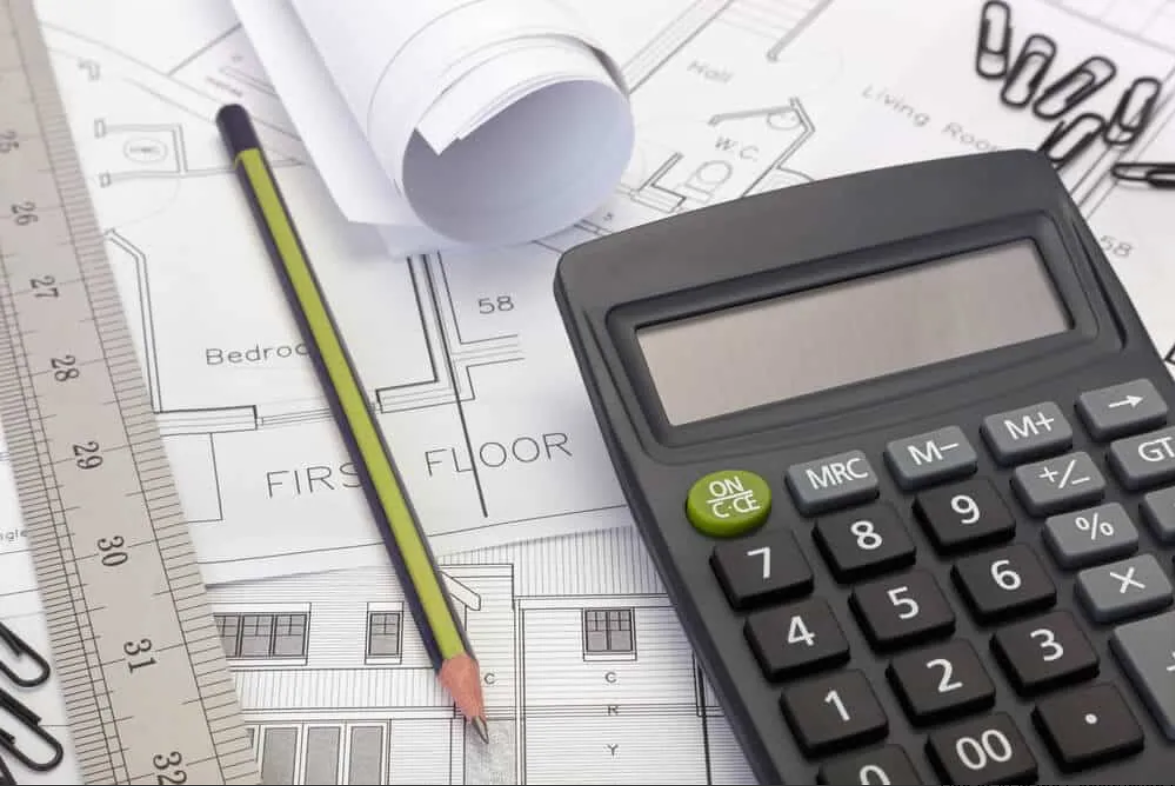
Tips for Creating an Accurate Material Takeoff
- Use the Right Tools: Employ specialized takeoff software or tools to enhance accuracy and efficiency.
- Double-Check Calculations: Verify all quantities and calculations to avoid errors.
- Consider Waste Factors: Account for material wastage during the takeoff process.
- Collaborate with Estimators: Work closely with estimators to ensure accurate pricing.
- Review and Update: Regularly review and update the takeoff as the project progresses.